Busbar System : ( POWERDUCT )
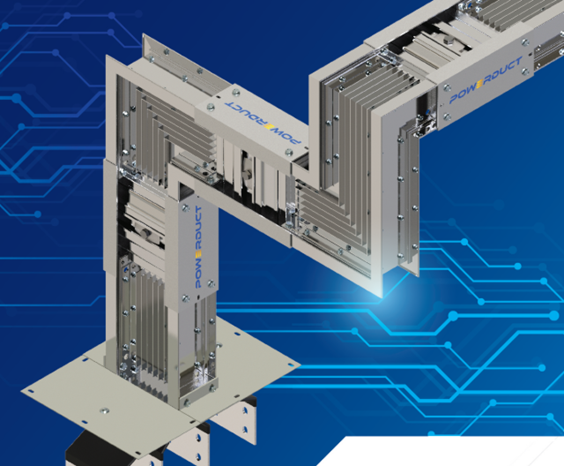
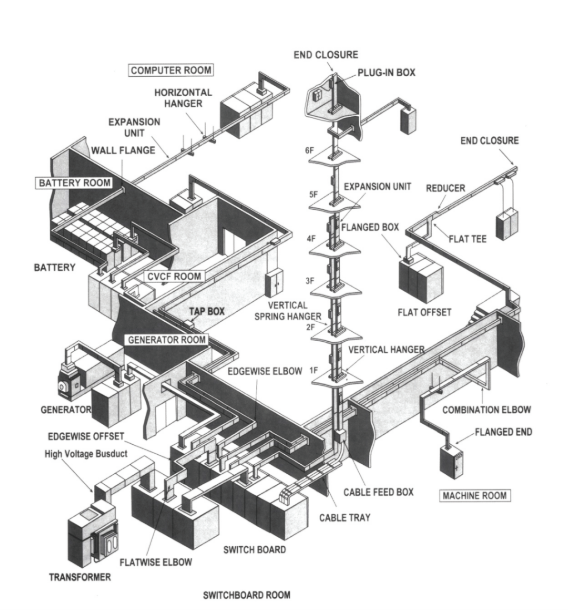
FJ Group is the Exclusive Agent for POWERDUCT Busbar system in UAE
POWERDUCT is ADQCC and SEWA certified. (Under Renew)
All the POWERDUCT busway product is designed and manufactured in compliance of the following standards:
IEC 60529
IEC 61439-6
UL 857
CSA 857
CSA C22.9 NO. 27-94
NEMA BUI
JIS 8364
All bus bars are manufactured from high electrical grade high conductivity electrolytic coppers which comply with international standard- BS1433/1432.
The copper composition of the bus bar is of 99.9% or conductivity in excess of 99% IACS.
Electroplated with tin on all contact surfaces. Optional silver plating is also available. This will improve conductivity more effectively.
All Busway are constructed in sandwich type which means no air gap shall exist between bus bars except at the joint. This can obtain lower impedance and better heat dissipation. Lower impedance means lower voltage drop.
The entire conductor also being insulated with epoxy powder (Hybrid Powder) coated which giving 100%water, rust and chemical resistance. Optional specification can be designed and fabricated to customer’s request.
Powerduct busway system enable you to optimize the energy usage and reduce unnecessary energy wastage which is a hidden cost. Better heat dissipation will provide cooler busway energizing. At the same time,
the busway has lower impedance and lower voltage drop if compared to the other competitors’ busway.
These features also include extremely low reactance due to non-magnetic housing and totally intimate contact of bus bars and housing.
Powerduct structure is designed to provide a very good short circuit protection. The short circuit has been certified by DEKRA (formerly known as KEMA) in accordance with IEC and BSEN Publication 61439-6
Bus bars are available in various configurations:
3P3W + Integral Ground
3P3W + 50% Internal Ground
3P3W + 100% Neutral + Integral Ground
3P3W + 100% Neutral + 50% Internal Ground
3P3W + 100% Neutral + 100% Internal Ground
3P3W + 200% Neutral + Integral Ground
3P3W + 200% Neutral + 50% Internal Ground
3P3W + 100% Internal Ground
Powerduct busway is constructed with extruded aluminum and is designed with cooling fin on both top and bottom. Benefits of such design are as follows:
Super Compact & Light Weight
Low Impedance
Greater heat dissipation
Better housing as Ground medium
Dust free
Corrosion free
Low Installation Cost.
This construction has been tested and has achieved the highest 60-cycle short circuit withstand ratings under the IEC and BSEN publication 61439-6 : 2012 approved by third party certification.
The enclosure has also been tested for ingress protection and has achieved the highest IP68 for standard feeder and IP55 for plug-in section
Insulation
The 130ºC Class B insulation is the primary insulation in all PPB conductors.
Optional Mylar and epoxy insulation (Hybrid).
155ºC Class F and 180ºC Class H is available upon customer’s request.
This epoxy is no hygroscopic, self-extinguishing and bonded directly to the bus bar thus eliminating any air gap between the insulation and bus bars.
Advantages of using epoxy insulation are as follows:
Able to withstand glitch and spikes in electrical system
Halogen free
Resistant against water and chemical
High thermal conductivity
High mechanical strength against impact and capable with standing heat shock
Cater for expansion and contraction during peak and off-peak hours
Long life compares to PVC and Mylar
Impervious to acids, alkalis, acetones, mechanical oils and lubricants
Thermal Indicator (optional):
Most of the busway manufacturer will have inspection covers to permit inspection of the joint periodically.
Powerduct newly designed thermal indicator will provide a more convenient for continual visual inspection whereby the thermal indicator will show a sign when the joint is overheating. This benefit from convenience visual inspection without opening the cover and save time from labor inspection.
Temperature Rise
Powerduct busway is capable of carrying its full rated current continuously in ambient condition of 95% relative humidity and maximum temperature of 50˚C without exceeding 55˚C temperature rise.
Powerduct tested to ambient 50ºC test